Customer Profile
The client in this case study faced numerous challenges with their existing boiler plant. The boilers needed to be updated and nearing the end of their serviceable life, making spare parts and critical components challenging to obtain. Additionally, their non-condensing design resulted in inefficiencies and non-compliance with current standards, leading to higher fuel costs. Finally, with one boiler already failing, the remaining two were at risk of imminent breakdown, requiring urgent action.
Requirements
Our client sought a comprehensive boiler plant upgrade encompassing several key aspects. Modernisation was crucial, requiring the replacement of outdated, inefficient boilers with advanced condensing units. Space limitations presented a challenge, necessitating creative solutions to optimise plant room utilisation and ensure adequate access. Addressing the condensation drainage needs of the new boilers was another critical consideration. Finally, the existing single-point flue discharge system, incompatible with condensing technology and prone to failure, demanded an upgrade to ensure optimal and reliable operation.
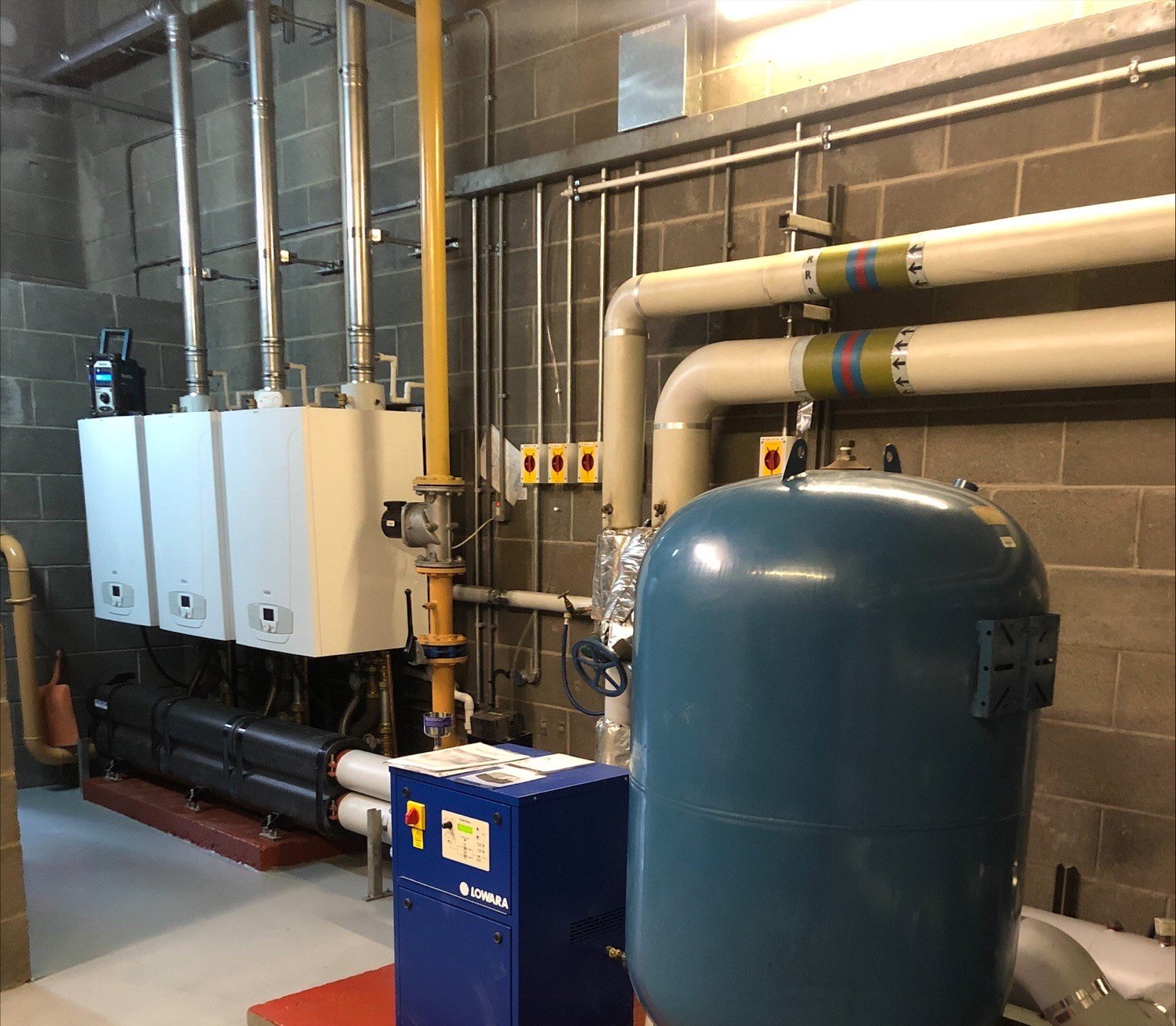
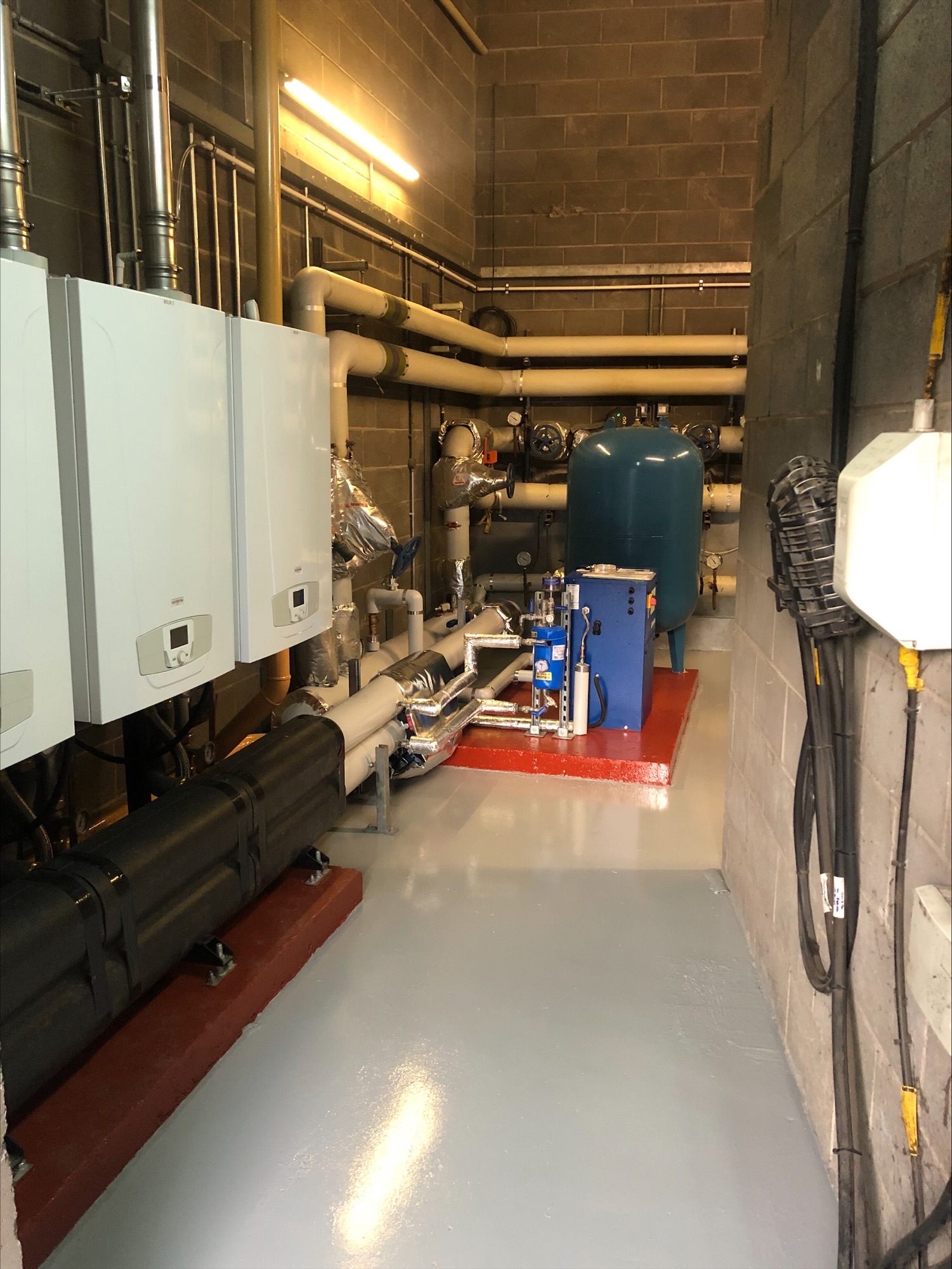
Solution
We proposed and implemented a comprehensive upgrade solution that included several key components:
We installed three 120 kW Potterton Sirius 3 condensing boilers, offering improved efficiency and lower minimum output compared to the previous system. To minimise downtime during installation, we meticulously rearranged the equipment layout within the plant room.
Our team custom-fabricated a low-loss header off-site to ensure optimal system performance. We further upgraded the flue system by installing three individual high-level condensing flues and connected both the flue and boiler condensate to the existing drainage system. Whilst on site we noticed the existing dosing pot and pressurisation unit were at the end of serviceable life and showing signs of corrosion and leaks. We ordered a new X-Pot, pressurisation unit and altered the pipework to suit the new equipment.
We seamlessly performed a gas line break-in, system changeover, and system commissioning on the agreed date. We removed the old equipment, cleaned the site, and painted the plant room floor and plinths to complete the project.
This upgrade resulted in a modern, efficient, and reliable boiler plant that significantly improved the client's heating system performance and reduced fuel costs by an estimated 20%.